ગ્રાઇન્ડીંગ ડિસ્ક વિવિધ ઉદ્યોગોમાં મુખ્ય ભૂમિકા ભજવે છે, જે સામગ્રીને આકાર આપવા અને પૂર્ણ કરવામાં મદદ કરે છે. જો કે, અન્ય કોઈપણ સાધનની જેમ, તેઓ તેમની કાર્યક્ષમતા અને પ્રદર્શનને અવરોધી શકે તેવી સમસ્યાઓથી મુક્ત નથી. આ લેખમાં, અમે સામાન્ય ગ્રાઇન્ડીંગ ડિસ્ક સમસ્યાઓનો અભ્યાસ કરીશું, તેમના મૂળ કારણોનું અન્વેષણ કરીશું અને સીમલેસ વર્કફ્લો માટે અસરકારક ઉકેલો પ્રદાન કરીશું.
પરિચય
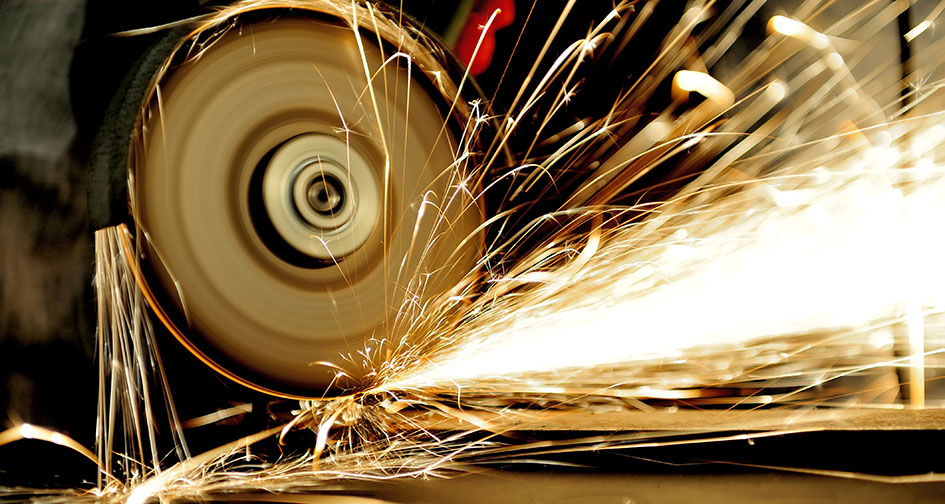
ગ્રાઇન્ડીંગ ડિસ્ક વિવિધ ઉદ્યોગોમાં મૂળભૂત ભૂમિકા ભજવે છે, જે સામગ્રી દૂર કરવા, આકાર આપવા અને ફિનિશિંગ પ્રક્રિયાઓ માટે આવશ્યક સાધનો તરીકે સેવા આપે છે. તેમના ઉપયોગને શ્રેષ્ઠ બનાવવા અને કાર્યક્ષમ કામગીરી સુનિશ્ચિત કરવા માટે તેમની વ્યાખ્યા, ઉદ્યોગોમાં મહત્વ અને સામાન્ય સમસ્યાઓને સમજવી મહત્વપૂર્ણ છે.
A. ગ્રાઇન્ડીંગ ડિસ્કની વ્યાખ્યા
ગ્રાઇન્ડીંગ ડિસ્ક એ ઘર્ષક સાધનો છે જેનો ઉપયોગ મશીનિંગ પ્રક્રિયાઓમાં સામગ્રીની સપાટીને કાપવા, ગ્રાઇન્ડ કરવા અથવા પોલિશ કરવા માટે થાય છે. આ ડિસ્કમાં સામાન્ય રીતે બેકિંગ સામગ્રી સાથે જોડાયેલા ઘર્ષક કણો હોય છે, જે એક ફરતું સાધન બનાવે છે જે વધારાની સામગ્રીને દૂર કરી શકે છે, સપાટીને સરળ બનાવી શકે છે અથવા ધારને તીક્ષ્ણ કરી શકે છે. તે વિવિધ આકારો અને કદમાં આવે છે, દરેક ચોક્કસ એપ્લિકેશનો માટે રચાયેલ છે.
B. વિવિધ ઉદ્યોગોમાં મહત્વ
ધાતુકામ ઉદ્યોગ:
ધાતુના ઉત્પાદન અને ઉત્પાદનમાં, ધાતુની સપાટીને આકાર આપવા, ડિબરિંગ કરવા અને ફિનિશ કરવા માટે ગ્રાઇન્ડીંગ ડિસ્ક મહત્વપૂર્ણ છે. ચોક્કસ પરિમાણો અને સપાટીની ગુણવત્તા પ્રાપ્ત કરવા માટે તેનો ઉપયોગ સામાન્ય રીતે એંગલ ગ્રાઇન્ડર સાથે થાય છે.
બાંધકામ ઉદ્યોગ:
બાંધકામ વ્યાવસાયિકો કોંક્રિટની સપાટી તૈયાર કરવા, ખરબચડી ધારને લીસું કરવા અને પથ્થર અને કોંક્રિટ જેવી સામગ્રીમાં રહેલી ખામીઓ દૂર કરવા જેવા કાર્યો માટે ગ્રાઇન્ડીંગ ડિસ્ક પર આધાર રાખે છે.
ઓટોમોટિવ ઉદ્યોગ:
ઓટોમોટિવ ક્ષેત્રમાં ગ્રાઇન્ડીંગ ડિસ્ક્સ એ સાધનોને શાર્પ કરવાથી લઈને ધાતુના ઘટકોને આકાર આપવા અને ફિનિશ કરવા સુધીના કાર્યો માટે આવશ્યક છે. તે ઓટોમોટિવ ભાગોની ચોકસાઇ અને ગુણવત્તામાં ફાળો આપે છે.
લાકડાકામ ઉદ્યોગ:
લાકડાના કામદારો લાકડાની સપાટીને આકાર આપવા અને સુંવાળી કરવા માટે ગ્રાઇન્ડીંગ ડિસ્કનો ઉપયોગ કરે છે. આ ડિસ્ક વધારાની સામગ્રી દૂર કરવામાં, આકારોને શુદ્ધ કરવામાં અને વધુ ફિનિશિંગ માટે લાકડાને તૈયાર કરવામાં અસરકારક છે.
સામાન્ય ઉત્પાદન:
ગ્રાઇન્ડીંગ ડિસ્કનો ઉપયોગ વિવિધ ઉત્પાદન પ્રક્રિયાઓમાં થાય છે જ્યાં ચોક્કસ સામગ્રી દૂર કરવાની જરૂર પડે છે, જે ઉચ્ચ-ગુણવત્તાવાળા ઘટકોના ઉત્પાદનમાં ફાળો આપે છે.
C. સામાન્ય સમસ્યાઓનો સામનો કરવો પડે છે
ડિસ્ક ઘસારો અને ઘર્ષણ:
સતત ઉપયોગથી ગ્રાઇન્ડીંગ ડિસ્ક ઘસાઈ શકે છે અને ઘર્ષણ થઈ શકે છે, જે તેની કામગીરીને અસર કરે છે. કાર્યક્ષમતા જાળવવા માટે નિયમિત નિરીક્ષણ અને રિપ્લેસમેન્ટ જરૂરી છે.
વધારે ગરમ થવું:
લાંબા સમય સુધી ઉપયોગ દરમિયાન વધુ પડતા ઘર્ષણથી વધુ ગરમ થઈ શકે છે, જે ડિસ્કની ટકાઉપણું અને ફિનિશ્ડ સપાટીની ગુણવત્તાને અસર કરે છે. યોગ્ય ઠંડકના પગલાં અને સમયાંતરે વિરામ જરૂરી છે.
ભરાઈ જવું:
ડિસ્કને ગ્રાઇન્ડ કરવાથી સામગ્રીના અવશેષો એકઠા થઈ શકે છે, જે તેમની અસરકારકતા ઘટાડે છે. નિયમિત સફાઈ અથવા એન્ટી-ક્લોગિંગ સુવિધાઓવાળી ડિસ્ક પસંદ કરવાથી આ સમસ્યાને રોકવામાં મદદ મળે છે.
કંપન અને ધ્રુજારી:
અસંતુલન અથવા અસમાન ઘસારાને કારણે કંપન અથવા ધ્રુજારી થઈ શકે છે, જે ફિનિશની ગુણવત્તા અને કામગીરીની સલામતી બંનેને અસર કરે છે. યોગ્ય ઇન્સ્ટોલેશન અને સંતુલન મહત્વપૂર્ણ છે.
ખોટી ડિસ્ક પસંદગી:
ચોક્કસ સામગ્રી અથવા એપ્લિકેશન માટે ખોટા પ્રકારની ગ્રાઇન્ડીંગ ડિસ્ક પસંદ કરવાથી બિનકાર્યક્ષમતા અને સંભવિત નુકસાન થઈ શકે છે. સામગ્રીની સુસંગતતાના આધારે યોગ્ય પસંદગી કરવી જરૂરી છે.
આ સાધનો પર આધાર રાખતા ઉદ્યોગો માટે ગ્રાઇન્ડીંગ ડિસ્ક સાથે સંકળાયેલી વ્યાખ્યા, મહત્વ અને સંભવિત પડકારોને સમજવું જરૂરી છે. સામાન્ય સમસ્યાઓને સંબોધીને અને યોગ્ય ઉપયોગ સુનિશ્ચિત કરીને, ઉદ્યોગો તેમના સંબંધિત એપ્લિકેશનોમાં ગ્રાઇન્ડીંગ ડિસ્કની અસરકારકતા મહત્તમ કરી શકે છે.
ગ્રાઇન્ડીંગ ડિસ્ક પર ઘસારો અને ફાટી જવું
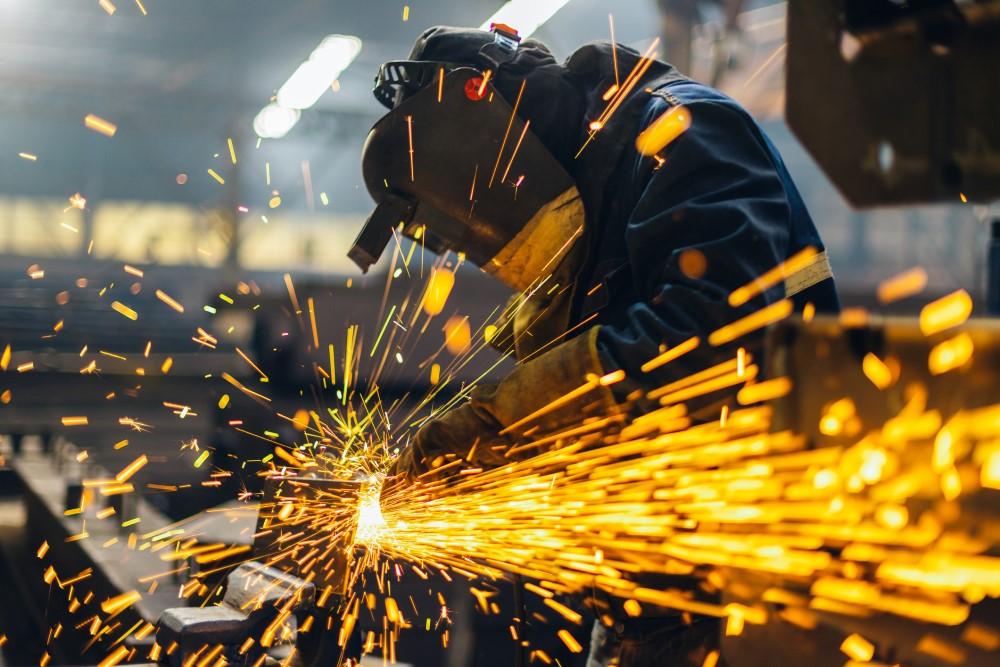
ગ્રાઇન્ડીંગ ડિસ્ક વિવિધ ઉદ્યોગોમાં આવશ્યક સાધનો છે, જે ધાતુના ઉત્પાદનથી લઈને કોંક્રિટ પોલિશિંગ સુધીના કાર્યો માટે જરૂરી ઘર્ષણ પૂરું પાડે છે. ગ્રાઇન્ડીંગ ડિસ્કના ઘસારામાં ફાળો આપતા પરિબળોને સમજવું તેમના પ્રદર્શનને શ્રેષ્ઠ બનાવવા અને સલામતી સુનિશ્ચિત કરવા માટે મહત્વપૂર્ણ છે.
સામગ્રીની કઠિનતા અને રચના:
કઠિનતામાં ફેરફાર:ગ્રાઇન્ડીંગ ડિસ્કમાં વિવિધ કઠિનતા સ્તરો ધરાવતી સામગ્રીનો સામનો કરવો પડે છે. ધાતુ અને કોંક્રિટ જેવા ઘર્ષક પદાર્થો કઠિનતામાં નોંધપાત્ર રીતે અલગ હોઈ શકે છે. કઠણ પદાર્થો સામે સતત ગ્રાઇન્ડીંગ કરવાથી ઘસારો વધે છે.
સામગ્રી રચના:ગ્રાઉન્ડિંગ કરતી સામગ્રીમાં ઘર્ષક તત્વોની હાજરી ગ્રાઇન્ડીંગ ડિસ્કના ઘસારાને અસર કરી શકે છે. ઘર્ષક કણો ડિસ્કના ઘસારાને ઝડપી બનાવી શકે છે.
ગ્રાઇન્ડીંગ પ્રેશર અને ફોર્સ:
અતિશય દબાણ:ગ્રાઇન્ડીંગ ડિસ્ક પર વધુ પડતું દબાણ કરવાથી ઝડપથી ઘસાઈ શકે છે. ડિસ્ક પર બિનજરૂરી તાણ ટાળવા માટે ચોક્કસ એપ્લિકેશન માટે ભલામણ કરેલ દબાણનો ઉપયોગ કરવો જરૂરી છે.
અપૂરતું બળ: બીજી બાજુ, અપૂરતા બળના કારણે લાંબા સમય સુધી પીસવાનું કામ થઈ શકે છે, જેના કારણે વધારાનું ઘર્ષણ અને ગરમી ઉત્પન્ન થઈ શકે છે, જેના કારણે ઘસારો થઈ શકે છે.
ડિસ્ક ગુણવત્તા અને રચના:
ઘર્ષક સામગ્રીની ગુણવત્તા:ગ્રાઇન્ડીંગ ડિસ્કમાં વપરાતા ઘર્ષક સામગ્રીની ગુણવત્તા તેના જીવનકાળને નોંધપાત્ર રીતે પ્રભાવિત કરે છે. ઉચ્ચ-ગુણવત્તાવાળા ઘર્ષક સામગ્રી ઘસારો પ્રતિકાર કરે છે અને લાંબા સમય સુધી તીક્ષ્ણતા જાળવી રાખે છે.
બોન્ડિંગ એજન્ટ:ઘર્ષક કણોને એકસાથે રાખનાર બોન્ડિંગ એજન્ટ મહત્વપૂર્ણ ભૂમિકા ભજવે છે. સારી રીતે ડિઝાઇન કરેલ બોન્ડિંગ એજન્ટ ડિસ્કની ટકાઉપણું વધારે છે.
કાર્ય પર્યાવરણની સ્થિતિઓ:
તાપમાન:ગ્રાઇન્ડીંગ દરમિયાન ઉત્પન્ન થતા ઊંચા તાપમાન ડિસ્કની રચનાને અસર કરી શકે છે. વધુ પડતી ગરમી બોન્ડિંગ એજન્ટને નબળી પાડે છે અને ઘસારાને વેગ આપે છે.
ભેજ અને દૂષકો:કામના વાતાવરણમાં ભેજ અથવા દૂષકોના સંપર્કમાં આવવાથી ગ્રાઇન્ડીંગ ડિસ્કની અખંડિતતાને અસર થઈ શકે છે, જેના કારણે તે ઝડપથી ઘસાઈ જાય છે.
ઓપરેટર ટેકનિક:
યોગ્ય તકનીક:ઓપરેટર કૌશલ્ય અને ટેકનિક ખૂબ જ મહત્વપૂર્ણ છે. અયોગ્ય ઉપયોગ, જેમ કે ખોટા ખૂણા પર પીસવું અથવા વધુ પડતું બળ વાપરવું, અસમાન ઘસારામાં ફાળો આપી શકે છે અને ડિસ્કની આયુષ્ય ઘટાડી શકે છે.
નિયમિત નિરીક્ષણો:ઓપરેટરોએ નિયમિતપણે ગ્રાઇન્ડીંગ ડિસ્કનું નિરીક્ષણ કરવું જોઈએ કે જેથી નુકસાન કે ઘસારાના કોઈ ચિહ્નો દેખાય. ચોક્કસ બિંદુથી વધુ ઘસારો દર્શાવતી ડિસ્ક તાત્કાલિક બદલવી જોઈએ.
ડિસ્ક કદ અને RPM સુસંગતતા:
યોગ્ય કદ:ગ્રાઇન્ડર માટે યોગ્ય ડિસ્ક કદનો ઉપયોગ કરવો ખૂબ જ મહત્વપૂર્ણ છે. ખોટી કદની ડિસ્ક અસમાન રીતે ઘસાઈ શકે છે અથવા સલામતી જોખમો ઉભા કરી શકે છે.
RPM સુસંગતતા:ગ્રાઇન્ડીંગ ડિસ્ક માટે ભલામણ કરેલ રિવોલ્યુશન પ્રતિ મિનિટ (RPM) નું પાલન શ્રેષ્ઠ કામગીરી સુનિશ્ચિત કરે છે અને અકાળ ઘસારો અટકાવે છે.
ઘસારો ઓછો કરવા માટે નિયમિત જાળવણી, ભલામણ કરેલ ઓપરેટિંગ શરતોનું પાલન અને કાર્ય માટે યોગ્ય ગ્રાઇન્ડીંગ ડિસ્ક પસંદ કરવી એ આવશ્યક પ્રથાઓ છે. ઘસારાને પ્રભાવિત કરતા પરિબળોને સમજીને, ઓપરેટરો ગ્રાઇન્ડીંગ ડિસ્કની આયુષ્ય અને કાર્યક્ષમતા વધારી શકે છે, જે સુરક્ષિત અને વધુ ઉત્પાદક ગ્રાઇન્ડીંગ કામગીરીમાં ફાળો આપે છે.
અસમાન ગ્રાઇન્ડીંગ
અસમાન ગ્રાઇન્ડીંગ એ એવી પરિસ્થિતિનો ઉલ્લેખ કરે છે જ્યાં સપાટીને ગ્રાઉન્ડ કરવામાં આવે ત્યારે તે સુસંગત અને સરળ પૂર્ણાહુતિ પ્રાપ્ત કરતી નથી. આ સમસ્યા વિવિધ કારણોસર ઊભી થઈ શકે છે અને વર્કપીસની ગુણવત્તાને અસર કરી શકે છે. અસમાન ગ્રાઇન્ડીંગમાં ફાળો આપતા સામાન્ય પરિબળો અને સંભવિત ઉકેલો અહીં આપેલા છે:
ખોટી ગ્રાઇન્ડીંગ વ્હીલ પસંદગી:
ઉકેલ:ખાતરી કરો કે ગ્રાઇન્ડીંગ વ્હીલ ગ્રાઉન્ડિંગ માટે યોગ્ય છે. વિવિધ સામગ્રીને ચોક્કસ ઘર્ષક ગુણધર્મોની જરૂર હોય છે. ઉપયોગ માટે યોગ્ય વ્હીલ પ્રકાર, ગ્રિટ કદ અને બોન્ડ પસંદ કરો.
અયોગ્ય વ્હીલ ડ્રેસિંગ:
કારણ:ગ્રાઇન્ડીંગ વ્હીલ જે યોગ્ય રીતે પહેરવામાં ન આવે તે અસમાન ઘસારો અને બિનઅસરકારક કટીંગ તરફ દોરી શકે છે.
ઉકેલ:ગ્રાઇન્ડીંગ વ્હીલનો આકાર જાળવી રાખવા અને કોઈપણ સંચિત કાટમાળ દૂર કરવા માટે તેને નિયમિતપણે ડ્રેસિંગ કરો. યોગ્ય ડ્રેસિંગ એક સુસંગત કટીંગ સપાટી સુનિશ્ચિત કરે છે.
અપૂરતું ગ્રાઇન્ડીંગ પ્રવાહી અથવા શીતક:
કારણ:ગ્રાઇન્ડીંગ પ્રવાહીનો અપૂરતો અથવા અયોગ્ય ઉપયોગ ઘર્ષણ અને ગરમીમાં વધારો કરી શકે છે, જેના કારણે અસમાન ગ્રાઇન્ડીંગ થાય છે.
ઉકેલ:ગરમી દૂર કરવા અને ઘર્ષણ ઘટાડવા માટે યોગ્ય ગ્રાઇન્ડીંગ પ્રવાહી અથવા શીતકનો ઉપયોગ કરો. સમાન પરિણામો પ્રાપ્ત કરવા માટે યોગ્ય ઠંડક જરૂરી છે.
ખોટા ગ્રાઇન્ડીંગ પરિમાણો:
કારણ:વધુ પડતી ગતિ, ફીડ રેટ અથવા કાપવાની ઊંડાઈ જેવા ખોટા ગ્રાઇન્ડીંગ પરિમાણોનો ઉપયોગ કરવાથી અસમાન ગ્રાઇન્ડીંગ થઈ શકે છે.
ઉકેલ:સામગ્રી અને એપ્લિકેશનની જરૂરિયાતો અનુસાર ગ્રાઇન્ડીંગ પરિમાણોને સમાયોજિત કરો. શ્રેષ્ઠ સેટિંગ્સ માટે ઉત્પાદકની ભલામણોનો સંદર્ભ લો.
ઘસાઈ ગયેલું ગ્રાઇન્ડીંગ વ્હીલ:
કારણ:ઘસાઈ ગયેલું ગ્રાઇન્ડીંગ વ્હીલ એકસરખી કટીંગ સપાટી પ્રદાન કરી શકતું નથી, જેના પરિણામે અસમાન ગ્રાઇન્ડીંગ થાય છે.
ઉકેલ:ગ્રાઇન્ડીંગ વ્હીલ તેના ઉપયોગના સમયગાળાના અંત સુધી પહોંચે ત્યારે તેને બદલો. ઘસારાના સંકેતો માટે નિયમિતપણે વ્હીલનું નિરીક્ષણ કરો.
અસમાન દબાણ અથવા ફીડ દર:
કારણ:ગ્રાઇન્ડીંગ દરમિયાન અસમાન દબાણ અથવા અસંગત ફીડ દરને કારણે સામગ્રી અનિયમિત રીતે દૂર થઈ શકે છે.
ઉકેલ:વર્કપીસ પર એકસમાન દબાણ લાગુ કરો અને એકસમાન ફીડ રેટ જાળવો. ઓપરેટર કૌશલ્ય અને વિગતો પર ધ્યાન આપવું ખૂબ જ મહત્વપૂર્ણ છે.
મશીન સમસ્યાઓ:
કારણ:ગ્રાઇન્ડીંગ મશીનમાં યાંત્રિક સમસ્યાઓ, જેમ કે ખોટી ગોઠવણી અથવા સ્પિન્ડલમાં સમસ્યાઓ, અસમાન ગ્રાઇન્ડીંગમાં પરિણમી શકે છે.
ઉકેલ:ગ્રાઇન્ડીંગ મશીનની નિયમિત જાળવણી તપાસ કરો. યોગ્ય કાર્યક્ષમતા સુનિશ્ચિત કરવા માટે કોઈપણ યાંત્રિક સમસ્યાઓનું તાત્કાલિક નિરાકરણ કરો.
વર્કપીસ ફિક્સરિંગ:
કારણ:ખરાબ રીતે સુરક્ષિત અથવા ખોટી રીતે ગોઠવાયેલ વર્કપીસ અસમાન ગ્રાઇન્ડીંગ તરફ દોરી શકે છે.
ઉકેલ:વર્કપીસનું યોગ્ય ફિક્સ્ચર અને ગોઠવણી સુનિશ્ચિત કરો. ગ્રાઇન્ડીંગ પ્રક્રિયા દરમિયાન હલનચલન અટકાવવા માટે તેને ચુસ્તપણે સુરક્ષિત કરો.
અસમાન ગ્રાઇન્ડીંગને સંબોધવા માટે યોગ્ય સાધનો સેટઅપ, યોગ્ય ઓપરેટિંગ પરિમાણો અને નિયમિત જાળવણી પદ્ધતિઓનું સંયોજન જરૂરી છે. ગ્રાઇન્ડીંગ એપ્લિકેશન્સમાં ઉચ્ચ-ગુણવત્તાવાળા અને સુસંગત પરિણામો પ્રાપ્ત કરવા માટે ઓપરેટરોને તાત્કાલિક સમસ્યાઓ ઓળખવા અને સુધારવા માટે તાલીમ આપવી જોઈએ. નિયમિત નિરીક્ષણો અને શ્રેષ્ઠ પ્રથાઓનું પાલન ગ્રાઇન્ડીંગ પ્રક્રિયા દરમિયાન કાર્યક્ષમ અને સમાન સામગ્રી દૂર કરવામાં ફાળો આપે છે.
ઓવરહિટીંગ સમસ્યાઓ
ગ્રાઇન્ડીંગ દરમિયાન વધુ પડતું ગરમી એક સામાન્ય સમસ્યા છે જે ગ્રાઇન્ડીંગ વ્હીલ અને વર્કપીસ બંનેના પ્રદર્શનને અસર કરી શકે છે. વધુ પડતી ગરમી વિવિધ સમસ્યાઓ તરફ દોરી શકે છે, જેમાં વ્હીલનું જીવન ઓછું થવું, વર્કપીસને થર્મલ નુકસાન અને એકંદરે ગ્રાઇન્ડીંગ કાર્યક્ષમતામાં ઘટાડો શામેલ છે. ઓવરહિટીંગ સમસ્યાઓના ઉકેલ માટે અહીં સંભવિત કારણો અને ઉકેલો છે:
ખોટા ગ્રાઇન્ડીંગ પરિમાણો:
કારણ:અયોગ્ય ગ્રાઇન્ડીંગ પરિમાણોનો ઉપયોગ, જેમ કે વધુ પડતી ગતિ, ફીડ રેટ અથવા કાપવાની ઊંડાઈ, વધારાની ગરમી ઉત્પન્ન કરી શકે છે.
ઉકેલ:ભલામણ કરેલ શ્રેણીમાં ગ્રાઇન્ડીંગ પરિમાણોને સમાયોજિત કરો. ગ્રાઇન્ડીંગ કરવામાં આવતી સામગ્રીના આધારે શ્રેષ્ઠ સેટિંગ્સ માટે ઉત્પાદકની માર્ગદર્શિકાનો સંપર્ક કરો.
અપૂરતી ઠંડક અથવા લુબ્રિકેશન:
કારણ:શીતક અથવા ગ્રાઇન્ડીંગ પ્રવાહીનો અપૂરતો ઉપયોગ ઘર્ષણ અને ગરમીમાં વધારો કરી શકે છે.
ઉકેલ:ગ્રાઇન્ડીંગ પ્રક્રિયા દરમિયાન શીતક અથવા લુબ્રિકન્ટનો પૂરતો પુરવઠો સુનિશ્ચિત કરો. યોગ્ય ઠંડક ગરમીને દૂર કરવામાં મદદ કરે છે અને થર્મલ નુકસાનને અટકાવે છે.
ખોટી વ્હીલ પસંદગી:
કારણ:સામગ્રીને ગ્રાઇન્ડ કરવા માટે અયોગ્ય સ્પષ્ટીકરણો સાથે ગ્રાઇન્ડીંગ વ્હીલ પસંદ કરવાથી વધુ ગરમ થઈ શકે છે.
ઉકેલ:ચોક્કસ ઉપયોગ માટે યોગ્ય ઘર્ષક પ્રકાર, ગ્રિટ કદ અને બોન્ડ ધરાવતું ગ્રાઇન્ડીંગ વ્હીલ પસંદ કરો. વ્હીલને સામગ્રી સાથે મેચ કરવાથી ગરમીનું ઉત્પાદન ઓછું થાય છે.
વર્કપીસ મટીરીયલ સમસ્યાઓ:
કારણ:કેટલીક સામગ્રી, ખાસ કરીને નબળી થર્મલ વાહકતા ધરાવતી સામગ્રી, ગ્રાઇન્ડીંગ દરમિયાન વધુ ગરમ થવાની સંભાવના વધારે હોય છે.
ઉકેલ:ઓછી થર્મલ વાહકતા ધરાવતી સામગ્રી માટે ગ્રાઇન્ડીંગ પરિમાણોને સમાયોજિત કરો. ગરમી-સંવેદનશીલ સામગ્રી માટે રચાયેલ વિશિષ્ટ ગ્રાઇન્ડીંગ વ્હીલનો ઉપયોગ કરવાનું વિચારો.
વ્હીલ ડ્રેસિંગ સમસ્યાઓ:
કારણ:ગ્રાઇન્ડીંગ વ્હીલની અનિયમિતતા અથવા અયોગ્ય ડ્રેસિંગ અસમાન સંપર્ક અને ગરમીના સંચય તરફ દોરી શકે છે.
ઉકેલ:ગ્રાઇન્ડીંગ વ્હીલનો આકાર જાળવી રાખવા માટે તેને નિયમિતપણે સજ્જ કરો અને કોઈપણ ગ્લેઝિંગ અથવા સંચિત કાટમાળ દૂર કરો. યોગ્ય રીતે સજ્જ વ્હીલ્સ સતત ગ્રાઇન્ડીંગ કામગીરી સુનિશ્ચિત કરે છે.
મશીનની અપૂરતી જાળવણી:
કારણ:ખરાબ રીતે જાળવણી કરાયેલ ગ્રાઇન્ડીંગ મશીનો ઓવરહિટીંગની સમસ્યાઓમાં ફાળો આપી શકે છે.
ઉકેલ:ગ્રાઇન્ડીંગ મશીનની નિયમિત જાળવણી કરો, જેમાં શીતક સિસ્ટમ્સ તપાસવી, વ્હીલ ડ્રેસિંગ સાધનોનું નિરીક્ષણ કરવું અને યોગ્ય ગોઠવણી સુનિશ્ચિત કરવી શામેલ છે. કોઈપણ યાંત્રિક સમસ્યાઓનું તાત્કાલિક નિરાકરણ લાવો.
અપૂરતો વ્હીલ શીતક પ્રવાહ:
કારણ:ગ્રાઇન્ડીંગ ઝોનમાં શીતકનો અપૂરતો પ્રવાહ ગરમીના વિસર્જનમાં ઘટાડો લાવી શકે છે.
ઉકેલ:શીતક ડિલિવરી સિસ્ટમ તપાસો અને ઑપ્ટિમાઇઝ કરો. ખાતરી કરો કે શીતક અસરકારક રીતે ગ્રાઇન્ડીંગ ઝોન સુધી પહોંચે છે જેથી ઠંડક કાર્યક્ષમતા જાળવી શકાય.
અતિશય ગ્રાઇન્ડીંગ સમય:
કારણ:વિરામ વિના લાંબા સમય સુધી ગ્રાઇન્ડીંગ સત્રો ગરમીના સંચયમાં ફાળો આપી શકે છે.
ઉકેલ:સમયાંતરે ગ્રાઇન્ડીંગનો ઉપયોગ કરો અને વધુ પડતી ગરમીનો સંચય અટકાવવા માટે વિરામ આપો. આ અભિગમ ખાસ કરીને મોટા અથવા પડકારજનક ગ્રાઇન્ડીંગ કાર્યો માટે મહત્વપૂર્ણ છે.
ગ્રાઇન્ડીંગમાં ઓવરહિટીંગની સમસ્યાઓનો ઉકેલ લાવવા માટે યોગ્ય સાધનો સેટઅપ, યોગ્ય ગ્રાઇન્ડીંગ પરિમાણો અને નિયમિત જાળવણી પદ્ધતિઓનો સમાવેશ કરીને એક વ્યાપક અભિગમની જરૂર છે. શ્રેષ્ઠ કામગીરી, વિસ્તૃત ટૂલ લાઇફ અને ઉચ્ચ-ગુણવત્તાવાળા પરિણામો સુનિશ્ચિત કરવા માટે ઓપરેટરોએ ગ્રાઇન્ડીંગ પ્રક્રિયા દરમિયાન ગરમી ઉત્પન્ન થવાનું નિરીક્ષણ અને નિયંત્રણ કરવું જોઈએ.
કંપનની ચિંતાઓ
ગ્રાઇન્ડીંગ કામગીરી દરમિયાન વધુ પડતા વાઇબ્રેશનથી સપાટીની ગુણવત્તામાં ઘટાડો, ટૂલના ઘસારામાં વધારો અને ગ્રાઇન્ડીંગ મશીનને સંભવિત નુકસાન સહિત વિવિધ સમસ્યાઓ થઈ શકે છે. ચોક્કસ અને કાર્યક્ષમ ગ્રાઇન્ડીંગ પ્રક્રિયાઓ પ્રાપ્ત કરવા માટે વાઇબ્રેશનની ચિંતાઓને સંબોધવી મહત્વપૂર્ણ છે. વાઇબ્રેશન સમસ્યાઓ ઘટાડવા માટેના સંભવિત કારણો અને ઉકેલો અહીં આપેલા છે:
અસમાન વ્હીલ ઘસારો:
કારણ:ગ્રાઇન્ડીંગ વ્હીલ પર અનિયમિત ઘસારો વર્કપીસ સાથે અસમાન સંપર્કમાં પરિણમી શકે છે, જેના કારણે કંપન થાય છે.
ઉકેલ:ગ્રાઇન્ડીંગ વ્હીલની સપાટીને સતત અને સપાટ રાખવા માટે તેનું નિયમિત નિરીક્ષણ કરો અને તેને સજ્જ કરો. વ્હીલની યોગ્ય જાળવણી કંપન ઘટાડવામાં મદદ કરે છે.
અસંતુલિત ગ્રાઇન્ડીંગ વ્હીલ:
કારણ:ગ્રાઇન્ડીંગ વ્હીલમાં અસંતુલન, ભલે તે અસમાન ઘસારાને કારણે હોય કે ઉત્પાદન ખામીને કારણે, કંપન તરફ દોરી શકે છે.
ઉકેલ:વ્હીલ બેલેન્સરનો ઉપયોગ કરીને ગ્રાઇન્ડીંગ વ્હીલને સંતુલિત કરો. સંતુલન વજનનું સમાન વિતરણ સુનિશ્ચિત કરે છે અને ઓપરેશન દરમિયાન કંપન ઘટાડે છે.
અપૂરતું મશીન કેલિબ્રેશન:
કારણ:વ્હીલ સ્પિન્ડલ અથવા વર્કટેબલ જેવા મશીનના ઘટકોનું નબળું કેલિબ્રેશન અથવા ખોટી ગોઠવણી, કંપનમાં ફાળો આપી શકે છે.
ઉકેલ:યોગ્ય કાર્યક્ષમતા સુનિશ્ચિત કરવા માટે મશીનના ઘટકોનું નિયમિત માપાંકન અને સંરેખણ કરો. મશીન સેટઅપ અને સંરેખણ માટે ઉત્પાદકની માર્ગદર્શિકા અનુસરો.
વર્કપીસ અસંતુલન:
કારણ:અસમાન અથવા અયોગ્ય રીતે સુરક્ષિત વર્કપીસ અસંતુલન પેદા કરી શકે છે અને કંપન પેદા કરી શકે છે.
ઉકેલ:વર્કપીસને યોગ્ય રીતે સુરક્ષિત કરો, ખાતરી કરો કે તે સમાન રીતે સ્થિત અને ક્લેમ્પ્ડ છે. ગ્રાઇન્ડીંગ પ્રક્રિયા શરૂ કરતા પહેલા કોઈપણ અસંતુલનની સમસ્યાઓનું નિરાકરણ લાવો.
ખોટી વ્હીલ પસંદગી:
કારણ:અયોગ્ય સ્પષ્ટીકરણો સાથે ગ્રાઇન્ડીંગ વ્હીલનો ઉપયોગ કરવાથી કંપન થઈ શકે છે.
ઉકેલ:સામગ્રીને ગ્રાઉન્ડ કરવા માટે યોગ્ય ઘર્ષક પ્રકાર, કપચીનું કદ અને બોન્ડ ધરાવતું ગ્રાઇન્ડીંગ વ્હીલ પસંદ કરો. વ્હીલને એપ્લિકેશન સાથે મેચ કરવાથી કંપન ઓછું થાય છે.
મશીનમાં ઘસારો અને ફાટવું:
કારણ:બેરિંગ્સ અથવા સ્પિન્ડલ્સ જેવા ઘસાઈ ગયેલા અથવા ક્ષતિગ્રસ્ત મશીન ઘટકો કંપનમાં ફાળો આપી શકે છે.
ઉકેલ:મશીનના ઘસાઈ ગયેલા ભાગોનું નિયમિતપણે નિરીક્ષણ કરો અને બદલો. યોગ્ય જાળવણી અતિશય કંપનને રોકવામાં મદદ કરે છે અને ગ્રાઇન્ડીંગ મશીનનું આયુષ્ય વધારે છે.
અપૂરતો શીતક પ્રવાહ:
કારણ:ગ્રાઇન્ડીંગ ઝોનમાં શીતકનો અપૂરતો પ્રવાહ ગરમીનું સંચય અને કંપનનું કારણ બની શકે છે.
ઉકેલ:યોગ્ય ઠંડક સુનિશ્ચિત કરવા માટે શીતક ડિલિવરી સિસ્ટમને ઑપ્ટિમાઇઝ કરો. અસરકારક ઠંડક થર્મલ વિસ્તરણ અને સંકોચનનું જોખમ ઘટાડે છે, જે કંપન તરફ દોરી શકે છે.
ટૂલ હોલ્ડર સમસ્યાઓ:
કારણ:ટૂલ હોલ્ડર અથવા સ્પિન્ડલ ઇન્ટરફેસમાં સમસ્યાઓ કંપન લાવી શકે છે.
ઉકેલ:ખાતરી કરો કે ટૂલ હોલ્ડર સુરક્ષિત રીતે માઉન્ટ થયેલ છે અને સ્પિન્ડલ સાથે યોગ્ય રીતે ગોઠવાયેલ છે. કંપન ઘટાડવા માટે ઉચ્ચ-ગુણવત્તાવાળા અને યોગ્ય રીતે જાળવણી કરાયેલ ટૂલ હોલ્ડર્સનો ઉપયોગ કરો.
મશીન ફાઉન્ડેશન:
કારણ:મશીનનો નબળો પાયો અથવા અપૂરતો ટેકો કંપનોને વધારી શકે છે.
ઉકેલ:ખાતરી કરો કે ગ્રાઇન્ડીંગ મશીન સ્થિર અને યોગ્ય રીતે ડિઝાઇન કરેલા પાયા પર સ્થાપિત થયેલ છે. મશીનમાં પ્રસારિત થતા કંપનોને ઘટાડવા માટે કોઈપણ માળખાકીય સમસ્યાઓનું નિરાકરણ કરો.
ગ્રાઇન્ડીંગમાં વાઇબ્રેશનની ચિંતાઓને અસરકારક રીતે સંબોધવા માટે યોગ્ય મશીન જાળવણી, વ્હીલ પસંદગી અને વર્કપીસ હેન્ડલિંગનું સંયોજન જરૂરી છે. ઓપરેટરોએ નિયમિત નિરીક્ષણ અને જાળવણી પદ્ધતિઓનો અમલ કરવો જોઈએ જેથી સમસ્યાઓને તાત્કાલિક ઓળખી શકાય અને તેનું નિરાકરણ કરી શકાય, જેના પરિણામે ગ્રાઇન્ડીંગ કામગીરી અને ગુણવત્તામાં સુધારો થાય.
ગ્રાઇન્ડીંગમાં લોડિંગ સમસ્યાઓ
ગ્રાઇન્ડીંગમાં લોડિંગ એ એવી ઘટના છે જ્યાં ગ્રાઇન્ડીંગ વ્હીલ પર ઘર્ષક અનાજ વચ્ચેની જગ્યાઓ ગ્રાઉન્ડિંગ સામગ્રીથી ભરાઈ જાય છે, જેના પરિણામે કાપવાની ક્રિયા ઓછી થાય છે અને ઘર્ષણ વધે છે. લોડિંગ ગ્રાઇન્ડીંગ પ્રક્રિયાની કાર્યક્ષમતા અને ગુણવત્તા પર નકારાત્મક અસર કરી શકે છે. લોડિંગ સમસ્યાઓના ઉકેલ માટે અહીં સંભવિત કારણો અને ઉકેલો છે:
સોફ્ટ વર્કપીસ સામગ્રી:
કારણ:નરમ પદાર્થોને પીસવાથી ઘર્ષક અનાજ ઝડપથી ભરાઈ શકે છે.
ઉકેલ:નરમ સામગ્રી પર કામ કરતી વખતે બરછટ કપચી અને ખુલ્લા માળખાવાળા ગ્રાઇન્ડીંગ વ્હીલનો ઉપયોગ કરો. આ ઝડપી લોડિંગને રોકવામાં મદદ કરે છે અને કાર્યક્ષમ રીતે ચિપ દૂર કરવાની મંજૂરી આપે છે.
સામગ્રી દૂષણ:
કારણ:વર્કપીસ સામગ્રીમાં હાજર દૂષકો, જેમ કે તેલ, ગ્રીસ અથવા શીતક અવશેષો, લોડિંગમાં ફાળો આપી શકે છે.
ઉકેલ:દૂષકો દૂર કરવા માટે પીસતા પહેલા વર્કપીસની યોગ્ય સફાઈની ખાતરી કરો. લોડિંગ ઘટાડવા માટે યોગ્ય કટીંગ પ્રવાહી અથવા શીતકનો ઉપયોગ કરો.
ખોટી શીતક એપ્લિકેશન:
કારણ:શીતકનો અપૂરતો અથવા અયોગ્ય ઉપયોગ અપૂરતી લ્યુબ્રિકેશન અને ઠંડક તરફ દોરી શકે છે, જેના પરિણામે લોડિંગ થઈ શકે છે.
ઉકેલ:શીતકના પ્રવાહ અને સાંદ્રતાને ઑપ્ટિમાઇઝ કરો. ખાતરી કરો કે શીતક અસરકારક રીતે ગ્રાઇન્ડીંગ ઝોન સુધી પહોંચે છે જેથી પ્રક્રિયાને લુબ્રિકેટ અને ઠંડુ કરી શકાય, જેથી લોડિંગ અટકાવી શકાય.
અપૂરતી વ્હીલ શાર્પનેસ:
કારણ:નીરસ અથવા ઘસાઈ ગયેલા ગ્રાઇન્ડીંગ વ્હીલ્સ લોડ થવાની સંભાવના વધારે હોય છે કારણ કે તે તેમની કટીંગ કાર્યક્ષમતા ગુમાવે છે.
ઉકેલ:ગ્રાઇન્ડીંગ વ્હીલની તીક્ષ્ણતા જાળવી રાખવા માટે તેને નિયમિતપણે ડ્રેસિંગ અને શાર્પ કરો. તાજા ઘર્ષક દાણા બહાર કાઢવા અને કટીંગ ક્રિયા વધારવા માટે વ્હીલ ડ્રેસરનો ઉપયોગ કરો.
ઓછી વ્હીલ ગતિ:
કારણ:ગ્રાઇન્ડીંગ વ્હીલને ઓછી ગતિએ ચલાવવાથી ચિપ્સ બહાર કાઢવા માટે પૂરતું કેન્દ્રત્યાગી બળ ન મળે, જેના કારણે લોડિંગ થાય છે.
ઉકેલ:ખાતરી કરો કે ગ્રાઇન્ડીંગ મશીન ચોક્કસ વ્હીલ અને વર્કપીસ સંયોજન માટે ભલામણ કરેલ ગતિએ કાર્ય કરે છે. વધુ ઝડપ ચીપને વધુ સારી રીતે દૂર કરવામાં મદદ કરી શકે છે.
અતિશય દબાણ:
કારણ:ગ્રાઇન્ડીંગ દરમિયાન વધુ પડતું દબાણ કરવાથી સામગ્રી ચક્રમાં બળજબરીથી ઘૂસી શકે છે, જેના કારણે લોડિંગ થઈ શકે છે.
ઉકેલ:મધ્યમ અને સુસંગત ગ્રાઇન્ડીંગ પ્રેશરનો ઉપયોગ કરો. ફીડ રેટને સમાયોજિત કરો જેથી વ્હીલ વધુ પડતા દબાણ વિના કાર્યક્ષમ રીતે કાપવામાં સક્ષમ બને જેના કારણે લોડિંગ થાય.
ખોટા વ્હીલ સ્પષ્ટીકરણો:
કારણ:સામગ્રીને ગ્રાઉન્ડ કરવા માટે ખોટી સ્પષ્ટીકરણો સાથે ગ્રાઇન્ડીંગ વ્હીલનો ઉપયોગ કરવાથી લોડિંગ થઈ શકે છે.
ઉકેલ:ચોક્કસ ઉપયોગ માટે યોગ્ય ઘર્ષક પ્રકાર, કપચીનું કદ અને બોન્ડ ધરાવતું ગ્રાઇન્ડીંગ વ્હીલ પસંદ કરો. વ્હીલને સામગ્રી સાથે મેચ કરવાથી લોડિંગ અટકાવવામાં મદદ મળે છે.
શીતકની અપૂરતી સફાઈ:
કારણ:દૂષિત અથવા જૂનું શીતક લોડિંગ સમસ્યાઓમાં ફાળો આપી શકે છે.
ઉકેલ:દૂષકોના સંચયને રોકવા માટે શીતકને નિયમિતપણે સાફ કરો અને બદલો. તાજું અને સ્વચ્છ શીતક લુબ્રિકેશન અને ઠંડક વધારે છે, જેનાથી લોડ થવાની શક્યતા ઓછી થાય છે.
અયોગ્ય ડ્રેસિંગ તકનીક:
કારણ:ગ્રાઇન્ડીંગ વ્હીલનું ખોટું ડ્રેસિંગ અનિયમિતતા અને લોડિંગ તરફ દોરી શકે છે.
ઉકેલ:યોગ્ય ડ્રેસિંગ ટૂલનો ઉપયોગ કરીને વ્હીલને યોગ્ય રીતે ડ્રેસ કરો. ખાતરી કરો કે વ્હીલ પ્રોફાઇલ સુસંગત છે અને લોડિંગ અટકાવવા માટે અનિયમિતતાઓથી મુક્ત છે.
લોડિંગ સમસ્યાઓને અસરકારક રીતે ઉકેલવા માટે યોગ્ય વ્હીલ પસંદગી, મશીન સેટઅપ અને જાળવણી પદ્ધતિઓનું સંયોજન શામેલ છે. ઓપરેટરોએ ભલામણ કરેલ પ્રક્રિયાઓનું પાલન કરવું જોઈએ, યોગ્ય ગ્રાઇન્ડિંગ પરિમાણોનો ઉપયોગ કરવો જોઈએ અને લોડિંગ ઘટાડવા અને ગ્રાઇન્ડિંગ કામગીરીને શ્રેષ્ઠ બનાવવા માટે નિયમિત વ્હીલ ડ્રેસિંગ લાગુ કરવું જોઈએ.
વિવિધ મેટલવર્કિંગ અને ફેબ્રિકેશન એપ્લિકેશન્સમાં શ્રેષ્ઠ પરિણામો પ્રાપ્ત કરવા માટે યોગ્ય ગ્રાઇન્ડીંગ ડિસ્ક પસંદ કરવી મહત્વપૂર્ણ છે. પસંદગી કામ કરવામાં આવી રહેલી સામગ્રી, ઇચ્છિત પૂર્ણાહુતિ અને ઉપયોગમાં લેવાતા ગ્રાઇન્ડરનો પ્રકાર જેવા પરિબળો પર આધારિત છે.
યોગ્ય ગ્રાઇન્ડીંગ ડિસ્ક પસંદ કરી રહ્યા છીએ
સામગ્રી સુસંગતતા:
ફેરસ ધાતુઓ (સ્ટીલ, આયર્ન):ખાસ કરીને ફેરસ ધાતુઓ માટે રચાયેલ ગ્રાઇન્ડીંગ ડિસ્કનો ઉપયોગ કરો. આ ડિસ્કમાં ઘણીવાર સ્ટીલની કઠિનતા માટે યોગ્ય ઘર્ષક પદાર્થો હોય છે અને તે લોડ થવાની સંભાવના ઓછી હોય છે.
બિન-લોહ ધાતુઓ (એલ્યુમિનિયમ, પિત્તળ):નરમ ધાતુઓ માટે યોગ્ય ઘર્ષક ધરાવતી ડિસ્ક પસંદ કરો જેથી ધાતુઓમાં ભરાવો ન થાય. એલ્યુમિનિયમ ઓક્સાઇડ અથવા સિલિકોન કાર્બાઇડ ડિસ્ક સામાન્ય પસંદગીઓ છે.
ઘર્ષક સામગ્રી:
એલ્યુમિનિયમ ઓક્સાઇડ:ફેરસ ધાતુઓ પર સામાન્ય હેતુ માટે પીસવા માટે યોગ્ય. તે ટકાઉ અને બહુમુખી છે.
ઝિર્કોનિયા એલ્યુમિના:ઉચ્ચ કટીંગ કાર્યક્ષમતા અને ટકાઉપણું પ્રદાન કરે છે, જે તેને ફેરસ અને નોન-ફેરસ ધાતુઓ પર આક્રમક ગ્રાઇન્ડીંગ માટે યોગ્ય બનાવે છે.
સિલિકોન કાર્બાઇડ:નોન-ફેરસ ધાતુઓ અને પથ્થરને પીસવા માટે આદર્શ. તે એલ્યુમિનિયમ ઓક્સાઇડ કરતાં તીક્ષ્ણ છે પરંતુ ઓછું ટકાઉ છે.
ગ્રિટનું કદ:
બરછટ ગ્રિટ (24-36):ઝડપી સ્ટોક દૂર કરવું અને હેવી-ડ્યુટી ગ્રાઇન્ડીંગ.
મધ્યમ ગ્રિટ (40-60):સ્ટોક દૂર કરવા અને સપાટી પૂર્ણાહુતિને સંતુલિત કરે છે.
ફાઇન ગ્રિટ (80-120):સપાટીની તૈયારી અને હળવા પીસવા માટે યોગ્ય, સરળ પૂર્ણાહુતિ પૂરી પાડે છે.
વ્હીલ પ્રકાર:
પ્રકાર 27 (ડિપ્રેસ્ડ સેન્ટર):સપાટ સપાટી સાથેની સ્ટાન્ડર્ડ ગ્રાઇન્ડીંગ ડિસ્ક, સપાટી ગ્રાઇન્ડીંગ અને ધારના કામ માટે આદર્શ.
પ્રકાર 29 (શંક્વાકાર):આક્રમક સ્ટોક દૂર કરવા અને સપાટીના વધુ સારા મિશ્રણ માટે કોણીય ડિઝાઇન.
પ્રકાર ૧ (સીધો):કટ-ઓફ એપ્લિકેશન માટે વપરાય છે. તે સચોટ કટીંગ માટે પાતળી પ્રોફાઇલ પૂરી પાડે છે.
અરજી:
ગ્રાઇન્ડીંગ:સામગ્રી દૂર કરવા અને આકાર આપવા માટે માનક ગ્રાઇન્ડીંગ ડિસ્ક.
કટીંગ:ધાતુને કાપવા માટે કટ-ઓફ વ્હીલ્સનો ઉપયોગ કરો, જેથી સીધી અને સ્વચ્છ ધાર મળે.
ફ્લૅપ ડિસ્ક:ગ્રાઇન્ડીંગ અને ફિનિશિંગ એક સાથે ભેગું કરો. સપાટીઓને મિશ્રિત કરવા અને સુંવાળી કરવા માટે યોગ્ય.
ગ્રાઇન્ડર સાથે સુસંગતતા:
ખાતરી કરો કે ગ્રાઇન્ડીંગ ડિસ્ક ઉપયોગમાં લેવાતા ગ્રાઇન્ડરના પ્રકાર અને ગતિ સાથે સુસંગત છે. ડિસ્કના મહત્તમ RPM (રિવોલ્યુશન પ્રતિ મિનિટ) માટે ઉત્પાદકની ભલામણો તપાસો.
કાર્ય વિશિષ્ટતા:
ભારે સ્ટોક દૂર કરવો:કાર્યક્ષમ રીતે સામગ્રી દૂર કરવા માટે બરછટ કપચી અને પ્રકાર 27 અથવા પ્રકાર 29 ડિસ્ક પસંદ કરો.
સપાટી પૂર્ણાહુતિ:સરળ ફિનિશ માટે ફ્લૅપ ડિસ્ક સાથે મધ્યમથી બારીક ગ્રિટ પસંદ કરો.
સલામતીની બાબતો:
સલામતી માર્ગદર્શિકાઓનું પાલન કરો, જેમાં સલામતી ચશ્મા અને મોજા જેવા યોગ્ય વ્યક્તિગત રક્ષણાત્મક ઉપકરણો (PPE) પહેરવાનો સમાવેશ થાય છે.
ટકાઉપણું અને સલામતી માટે પ્રબલિત ડિસ્ક પસંદ કરો.
બ્રાન્ડ અને ગુણવત્તા:
ગુણવત્તા અને સુસંગતતા માટે જાણીતા પ્રતિષ્ઠિત બ્રાન્ડ્સમાંથી ડિસ્ક પસંદ કરો. ઉચ્ચ-ગુણવત્તાવાળી ડિસ્ક વધુ સારી કામગીરી અને ટકાઉપણું પ્રદાન કરે છે.
ખર્ચની વિચારણા:
ગ્રાઇન્ડીંગ ડિસ્કના અપેક્ષિત આયુષ્ય અને પ્રદર્શન સાથે પ્રારંભિક ખર્ચનું સંતુલન બનાવો. ઉચ્ચ-ગુણવત્તાવાળી ડિસ્કની પ્રારંભિક કિંમત વધુ હોઈ શકે છે પરંતુ સમય જતાં તે વધુ સારી કિંમત પ્રદાન કરી શકે છે.
આ પરિબળોને ધ્યાનમાં લઈને, ઓપરેટરો તેમના ચોક્કસ ઉપયોગો માટે યોગ્ય ગ્રાઇન્ડીંગ ડિસ્ક પસંદ કરી શકે છે, કાર્યક્ષમતા, સલામતી અને શ્રેષ્ઠ પરિણામોની ખાતરી કરી શકે છે.
નિષ્કર્ષ
નિષ્કર્ષમાં, યોગ્ય ગ્રાઇન્ડીંગ ડિસ્ક પસંદ કરવી એ સફળ મેટલવર્કિંગ અને ફેબ્રિકેશન પરિણામો પ્રાપ્ત કરવા માટે એક મહત્વપૂર્ણ પાસું છે. પસંદગી વિવિધ પરિબળો પર આધાર રાખે છે જેમ કે કામ કરવામાં આવી રહેલી સામગ્રી, ઇચ્છિત પૂર્ણાહુતિ અને ઉપયોગમાં લેવાતા ગ્રાઇન્ડરનો પ્રકાર. સામગ્રીની સુસંગતતા, ઘર્ષક પ્રકાર, ગ્રિટનું કદ, વ્હીલ પ્રકાર, એપ્લિકેશન, ગ્રાઇન્ડર સુસંગતતા, કાર્ય વિશિષ્ટતા, સલામતી, બ્રાન્ડ ગુણવત્તા અને કિંમતને ધ્યાનમાં લઈને, ઓપરેટરો તેમની ગ્રાઇન્ડીંગ પ્રક્રિયાઓમાં કાર્યક્ષમતા અને સલામતી વધારવા માટે જાણકાર નિર્ણયો લઈ શકે છે.
સલામતી માર્ગદર્શિકાનું પાલન કરવું, યોગ્ય વ્યક્તિગત રક્ષણાત્મક ઉપકરણો પહેરવા અને ગ્રાઇન્ડર અને ડિસ્ક સુસંગતતા માટે ઉત્પાદકની ભલામણોનું પાલન કરવું આવશ્યક છે. ભલે તે ભારે સ્ટોક દૂર કરવા, સપાટીને પૂર્ણ કરવા અથવા કટીંગ એપ્લિકેશન માટે હોય, યોગ્ય ગ્રાઇન્ડિંગ ડિસ્ક કાર્યની ગુણવત્તા અને કાર્યક્ષમતા પર નોંધપાત્ર અસર કરી શકે છે.
વધુમાં, ઘસારાની સમયાંતરે તપાસ, ઓવરહિટીંગ અને વાઇબ્રેશન જેવી સમસ્યાઓનું નિરાકરણ, અને લોડિંગ સમસ્યાઓને સમજવાથી ગ્રાઇન્ડીંગ ડિસ્કનું જીવન લંબાવવામાં અને સતત કામગીરી સુનિશ્ચિત કરવામાં ફાળો મળે છે.
સારાંશમાં, ગ્રાઇન્ડીંગ ડિસ્ક પસંદ કરવા, ઉપયોગ કરવા અને જાળવવા માટે સારી રીતે જાણકાર અને વ્યવસ્થિત અભિગમ શ્રેષ્ઠ પરિણામો પ્રાપ્ત કરવા, ઉત્પાદકતા વધારવા અને સલામત કાર્યકારી વાતાવરણ સુનિશ્ચિત કરવા માટે ચાવીરૂપ છે.
પોસ્ટ સમય: જાન્યુઆરી-૧૨-૨૦૨૪